Inverse engineering
Initial design stages of support structures for wind turbines are characterised by the reduced information of the RNA and the controller available. This circumstance obstructs the optimisation of earliest system designs considering an holistic approach.
However, inverse engineering techniques allow the development of wind turbine models that mimic the dynamic behaviour of a commercial RNA and controller set with reduced information as starting point. The developed models are in line with the recommendations of international standards to perform coupled analysis to assess the integrated loads of wind turbines.
remove the bottlenecks of your wind project!
Rotor aerodynamics
Due to the importance of the aerodynamic loads on the design of a support structure, it is relevant for a project to start with high quality approaches of the expected loads.
For the development of the rotor and blades, few inputs are needed:
-
- Hub diameter, blades length, tilt angle and blades coning
- Objective wind turbine steady-state performance curves
- Airfoil family information speed-ups the process
Upwind and downwind horizontal-axis and vertical-axis wind turbines
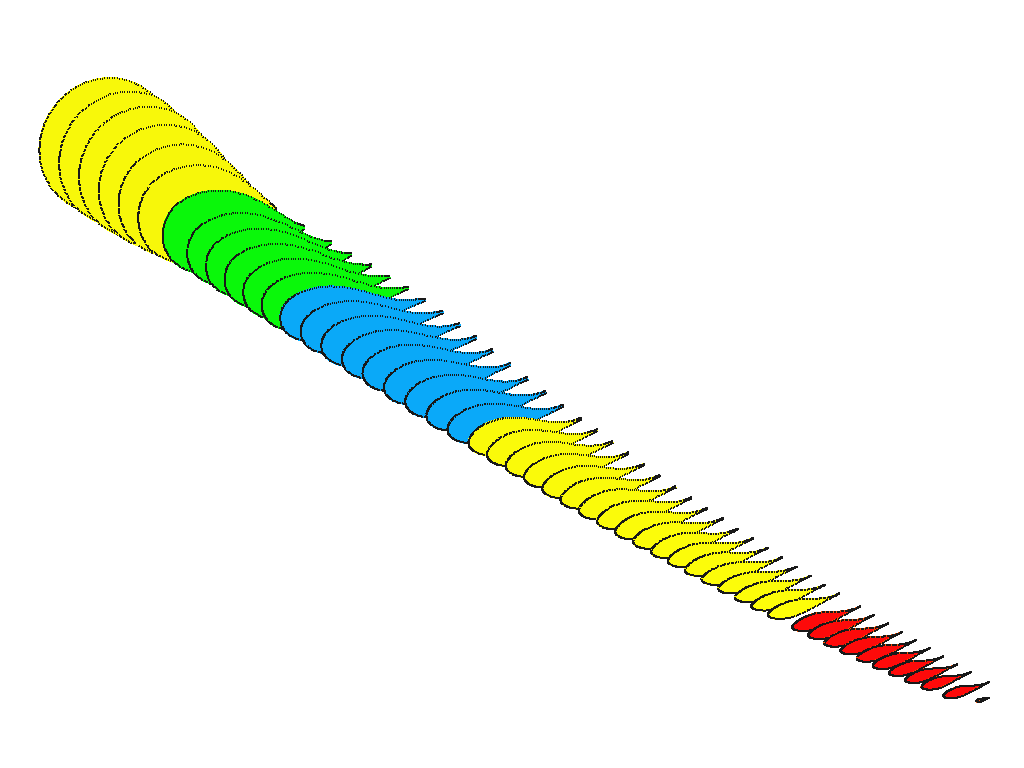
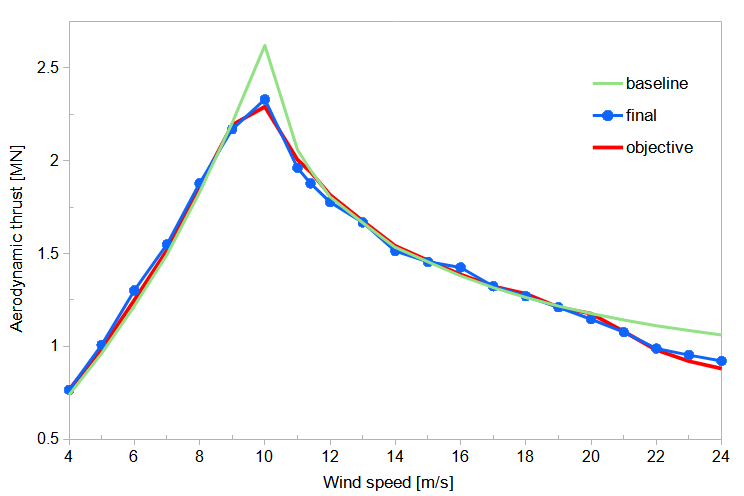
Wind turbine controller
A fine representation of the wind turbine servodynamics is critical to mimic the dynamic behaviour of the full system and thus, in the determination of wind turbine components life.
Required minimum information:
-
- Drivetrain and generator information
- Objective wind turbine steady-state performance curves
Data analysis
Data analysis plays an important role in inverse engineering tasks. In eureka! we combine traditional analysis techniques, system properties identification techniques and numerical modelling that can be, for example, applied to:
-
- Determine the natural frequencies and damping of a system
- Update the numerical models in which rely the digital twin of an operating system
- Feed a machine-learning process